E社はISOを取得していました。
文書管理は、「紙」中心で運用を行っていました。
ISO事務局は品質管理室に設置していました。
マニュアルの最新版管理は、サーバー共有ホルダーを使っていました。
アクセス権限を付与して管理していました。
手順書の最新版管理は、部門ごとサーバー共有ホルダーを使っていました。
アクセス権限を付与して管理していました。
記録管理は、部門ごとに記録し、「紙」「ファイル綴じ」保管していました。
【改善前 困っている点】
(1) 膨大は記録保管の場所(スペース)を確保していました。
(2) 人手不足で「紙」「ファイル綴じ」保管の背表紙印字やタグ管理が
出来ていませんでした。
(3) 審査やサーベランス前に残業をして「紙」「ファイル綴じ」保管の
整備を行っていました。
(4) ISO記録の中には、出来高等「タイムリー」に把握したい
データ、「利益」に直結するデータが含まれたいました。
(5)「利益」に直結するデータはエクセルに再入力して月例会議で
使っていました。
毎日の出来高把握は遅れていました。
改善活動も、後手後手に回っていました。
現場任せの改善活動でした。
(生産本部と現場のバラバラ間がありました)
(6)「仕掛品の管理」はルールが浸透せず、利益管理、キャッシュ
フロー管理がブレ困っていました。
「仕掛品」置き場も曖昧でした。
仕掛品を廃棄(ロス)と計算していました。
隠れ仕掛品を使い生産をしていました。
【改善後 アプリ化】
E社専用ISOアプリのコンサルティング支援を行いました。
(1) 記録は、「紙」のまま運用と「アプリ化」に区分しました。
(2) 記録の「紙」のまま運用は、水・油・温度等PC・スマホが
馴染まない作業場としました。
(3) 「アプリ化」運用は、『利益に直結する』出来高データを
当日把握することからスタートしました。
出来高データ把握後に「稼働率」「歩留まり」へ移行して
いきました。
(4)「仕掛品の管理」はルールを簡単に決めました。
簡単なルールとは、「仕掛品」置き場を決めました。
①ラインテープを貼り置き場決めました。
②看板を設置しました。
③当日出た仕掛品の写真を「アプリ」で撮影
「アプリ」に数量入力 としました。
④仕掛品の数量はアバウトでも良いことにしました。
仕掛品には、
A)生産ロットごとに生じる端数分も含まれていました。
B)共通品・規格品もあり他製品で使えるものもありました。
C)規格外で使えないものもありました。
【成果】
(1)出来高管理が早くなりました。
(2)仕掛品の把握が出来るようになりました。
(3)生産本部も含めた改善活動が早くなりました。
(4)利益管理、キャッシュフロー管理のブレが少なくたってきました。
【今後の取り組み】
(1)改善活動による更なる利益アップ
(2)工程ごとの利益に影響するデータ把握
(3)利益管理、キャッシュフロー管理の精度アップ
(4)利益を社員に還元するやり方の改定
待遇改善並びに還元のスピードも速くする
(週単位・月単位還元へ挑戦)
引き抜きも含め優秀人材確保
【こぼれ話】
社員の方へ聞きました。
質問:ペーパーレス化と社員への利益還元どちらを優先しますか?
回答:「社員への利益還元」
アプリのスマホ・タブレットの入力画面です。
↓画像をクリックすると拡大画面になります
———————————————————————————————–
アプリのPC集計画面です。クロス集計し出来高を
タイムリーに把握出来るようになりました。
↓画像をクリックすると拡大画面になります
№13.ISO記録データの有効活用 収益に結び付けよう
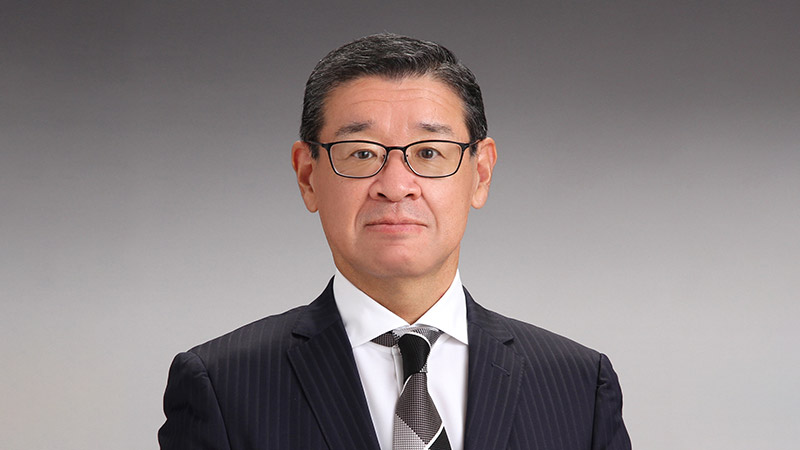