F社はメーカーです。
工程別に不良(廃棄)数量のデータをとっていました。
機械別、機械のエラー別にデータをとって改善活動に結び付けたいと考えていました。
【改善前】
(1)工程別の不良(廃棄)のデータのみ取得
(2)機械別、機械のエラー別データは未取得
(3)集計は1回/月
(4)過去に専用システムで廃棄データ集計を試みました。
現場でいつも使っている言葉や単語でなかった為
集計ミスが連発しました。
以後集計することや改善活動に消極的になってしまっていました。
<記録表 サンプル>
【改善後】
F社用の改善アプリ導入コンサルティングをご支援しました。
(1)機械別、機械のエラー別の不良(廃棄)データ取得が出来ました。
<集計フォーマット>
(2)データは、タイムリーに共有出来るようになりました。
(3)集計は、1回/月→1回/日、累計で月中でも把握できるようになりました。
早く対策を打つことが出来るようになりました。
(4)機械別エラーが「データ」としてわかる為、
早くしかもポイントを絞って改善対対策を打つことが可能となりました。
(5)改善の効果確認も1回/日で出来るようになりました。
(6)不良(廃棄)情報を1日/日 グラフ化して掲示出来るようになりました。
<自動グラフ作成、社内コミュニケーションサイトに自動貼り付け>
【止めたこと】
手書き記録の表計算ソフトへの再入力
【止めて良かったこと】
文字が読み取れない、読み間違いによる入力間違いが極端に少なくなった
入力そのものの間違いがなくなった
経営コンサルタントのワンポイントレッスン
(1)不良品(廃棄物)の写真撮影=証拠写真
データと不良(廃棄物)映像を一元管理するようコンサルティングしました。
(2)映像を使うことにより不良原因がより明確に判るようになりました。
№15 F社の改善活動、収益アップ活動
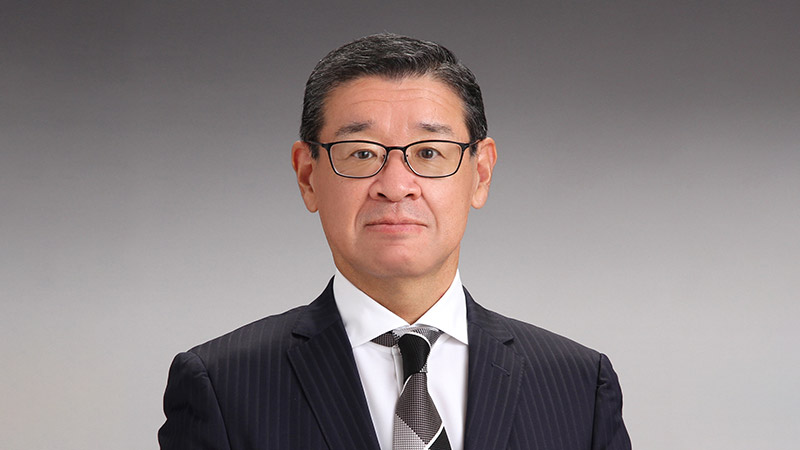